设备管理指标分析
设备故障率
管理概念:
关于设备故障率这个概念,所有设备管理者都会提到的概念,大家都会非常关注设备故障率指标,但当我们真正认真提出该指标的概念,管理目标,管理有效性的时候,大家都才感觉到迷茫,才认识到这个概念被自己提起,主要还是行业的一个惯性传递,自己还没有真正理解该指标!“故障率”从字面上可以理解为“设备出现故障的概率或者比率”,总结一下,行业内经常性有以下提法:
定义一:具体时刻发生故障的设备台数占投入使用设备台数的百分比值。
定义二:单位时间内发生过故障的设备台数占投入使用设备台数的百分比值。
定义三:单位时间内设备发生故障的次数。
定义四:单位时间内设备故障停用的时间占设备目标生产/工作时间的百分比值。
计算方式:
定义一:故障率=(故障台数/设备总台数)*100%;
定义二:故障率=(故障台数/设备总台数)*100%;
定义三:故障率=故障停机时间总和/(单台工作时间*设备总台数)*100%;
定义四:故障率=故障次数总和;
设备总数可以根据我们对考核者的考核要求来定,当设备总数是1的时候,就是单台设备的故障率。
管理目标:
提出设备故障率的指标,我们认为主要体现设备的失效状态和对生产的影响情况,同时考核相关管理维护人员的设备维护状态的水平和控制设备状态的能力。通过该指标,推动管理者加强管理,首先减少设备对生产影响,保证企业生产效益;然后加强设备维护,减少故障维修带来的一系列的备件存储、(紧急)采购、紧急人工等维修成本。故障率指标针对的可以是具体一台设备、一类设备;同时可以是管理者的所有设备、也可是管理者的部分重点设备。
管理分析:
讨论故障率,首先需要对故障进行定义,设备发生什么样的情况,归为故障,在《设备管理维修术语》一书中,将故障定义为“设备丧失规定的功能”。这一概念可包括如下内容:由于设备自身或者内部部件原因导致出现1、立即丧失其生产功能的状态,即为停机状态;2,设备性能降低,无法生产合格产品的状态。
定义一表达设备的故障率,体现的是一个时刻的设备故障状态,企业资产管理的角度上来说,我们应该关注重要设备的即时状态,让资产责任人有压力与动力去维护好设备,保持所有时刻的设备状态,但就实际上来说,该要求也给予了责任人一个管理投机的可能,赌博在管理者考核的时候,所负责的设备状态可能就是在非故障状态,而不会努力去作好设备维护的工作。用定义一作为指标来考核,随机性、偶然性很大,所以一些企业就把考核点定义在每月月末的固定时间,所有责任者就会在考核点到的时候全力去保持或者恢复设备的状态,这有一定的积极意义,但这样会掩盖考核期过程中管理设备出现的故障,丢掉了设备状态的真实性。总体来说,定义一应该是管理者关注的内容,对实现管理目标有一定意义,但如果要作为考核指标,缺陷大于指导意义,很难操作与推行。适合管理人手不够、管理统计记录手段薄弱的管理阶段和企业的简单管理。
定义二表达设备的故障率,体现的是一个阶段发生过的故障设备占所有考核范围设备的总数,在考核期内,只要出现一次故障,该设备就被纳入考核范围,相比定义一考核其中一个时点,要合理一些,定义二有一个缺陷,就是对于具体一台设备,在考核周期内出现故障超过1次,就忽略了多次停机对生产影响和成本的责任,责任人对考核期内已出现故障设备的关注就会减弱。
定义三表达设备的故障率,采用简单记数方法来记录考核期内设备的每一次故障,这种方法貌似简单,其实从设备责任者的角度来说,还真有其合理性:出现设备故障,主要原因是设备维护的不到位,无论对生产的影响有多大,对成本的影响有多大,都是设备责任者的问题,出现一次,就应该考核一次。当然,就管理目标,我们还是要在有限的企业资源基础上减少对生产的影响和成本的影响,这是定义三缺陷的地方。
定义四表达设备的故障率,考虑了故障对企业经营根本-生产的影响,对每次故障的停机时间进行统计,该指标从数字上,能够让管理者比较清楚当前设备状态对企业经营目标的影响有多大,更能够客观的指导管理决策。当然该指标对现场工作记录提出了更高的要求,要准确记录故障的起点时间和解决故障的终点时间,同时要求按照具体设备、设备类别、责任者进行统计,尤其是设备量很大的时候,对管理工具提出了一定要求。
有效性总结
对于设备故障率这个指标,无论采用上面那一种计算方式,具体数据都来自设备使用与维护一线工作人员,而我们考核的责任主体,又常常就是设备使用者或则设备维护者自身,所以,信息如何被真实反映,就是我们管理者必须认真考虑的问题,对着一个无真实性可控的指标进行考核,我们也只是在粉饰太平,只是在浪费时间,在自欺欺人。我们在好几个企业中都有类似发现,从一线管理者的工作方法、管理思路、检修费用、生产产量等角度去分析,我们认为管理好的一线管理者,他们上报的设备故障率居然要比其它同等角度反馈信息差好多的部门要高几许,实际现场调查设备状况和我们推理得到的结果是一致,为了搞清楚这种矛盾情况出现的原因,就召集过来当面沟通,他说,“就我提报的故障率,是我们现场实际的数据,我也不敢去做假,因为还有相关其他信息进行限制,所以我只有实情实报”。而他管理者也有不泛坦率者这样说:“我没有办法控制故障,整天都在忙碌,所以你们需要什么数字,我只有到时候就给你们什么数字,也考虑不过来上报数据的合理性,如果按照实情汇报,还不罚倒我啊,反正如果查出来,在认罚也一样!”。
所以,选择考核指标,我们首先要考虑我们获取信息、统计信息的有效性和可控性,没有这个前提,我们玩的就是简单的数字拼凑游戏,没有管理效果可言。
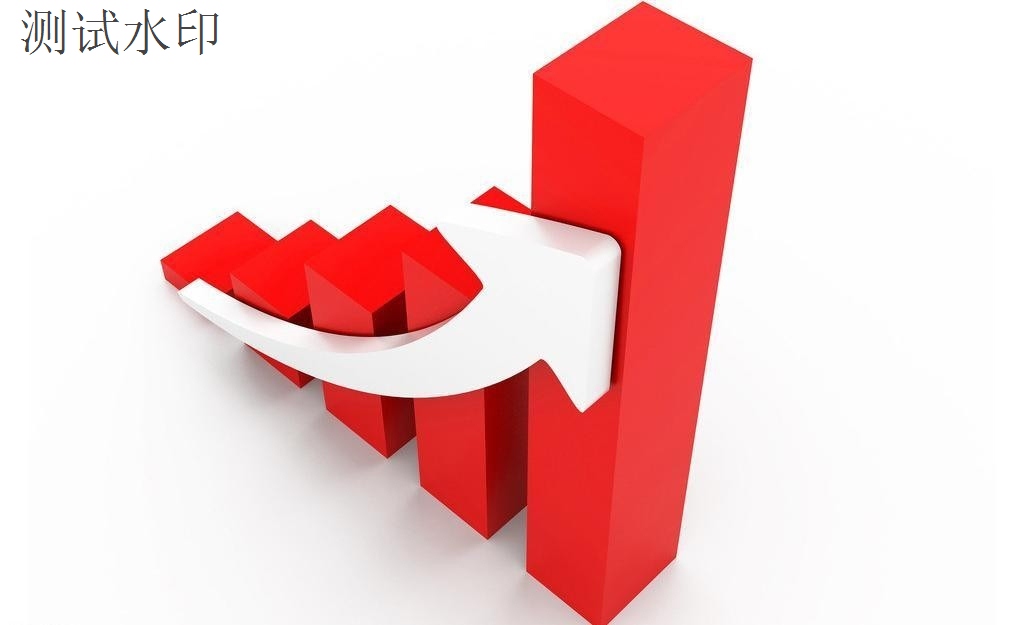
平均无故障间隔时间
平均无故障间隔时间,即为“Mean Time Between Failure”,简写为“MTBF”,这是衡量设备可靠性的很重要的指标,尤其是对产品/设备制造商来说,我们在这里不是作为生产产品可靠性的理论研究,生产产品可靠性计算会比较复杂,利用微积分来计算,就设备管理的角度,我们没有必要花这样大的成本来计算,我们的目标是对设备投入使用后的效果性分析,是从结果入手进行统计比较。
管理概念:
定义一:平均无故障间隔时间:在规定期限内,所有设备无故障工作时间的平均值,其计量单位通常采用小时。
定义二:平均无故障间隔时间:在规定期限内,每设备无故障工作时间的平均值,其计量单位通常采用小时。
计算方式:
定义一:MTBF=(设备总数*日标准工作小时*日期天数)/(故障次数+1);
或者
MTBF=(设备总数*日标准工作小时*日期天数-设备故障停机小时总和)/(故障次数+1);
或者
MTBF=(设备工作小时总和)/(故障次数+1);
出现三种计算方法,主要是否考虑具体每次设备故障停机时间对计算的影响,这根据企业设备故障特征来区别对待。
公式里分子至于为什么是“故障次数+1”,其实最简单的理解,如果只有1次故障,就是这次故障把设备工作时间分成两个部分,时间间隔就是除以“2”,如果没有故障,分子就是“1”,结果就是这段时间的整段时间是其无故障间隔时间。
当然,设备总台数是1的时候,就是单台设备的平均无故障间隔时间。
具体计算举例说明如下:
10台设备,每天工作20小时,工作一个月后有5台失效,MTBF是多少?
答案:MTBF=(10*20*30)/(5+1)=1000小时。
如果加上条件,每次失效后需要60小时才可以恢复,MTBF是多少?
答案:MTBF=((10*20*30)-5*60)/(5+1)=950小时。
定义二:
MTBF=(设备总数*日标准工作小时*日期天数)/((故障次数/设备总台数+1)*设备台数);;
或者
MTBF=(设备总数*日标准工作小时*日期天数-设备故障停机小时总和)/((故障次数/设备总台数+1)*设备台数);
或者
MTBF=(设备工作小时总和)/((故障次数/设备总台数+1)*设备台数);
具体计算举例说明如下:
10台设备,每天工作20小时,工作一个月后有5台失效,MTBF是多少?
答案:MTBF=(10*20*30)/((5/10+1)*10)=400小时。
这就意味着这类设备在每月600小时的工作时间内,每台设备能够持续坚持400小时无故障工作。
如果加上条件,每次失效后需要60小时才可以恢复,MTBF是多少?
答案:MTBF=((10*20*30)-5*60)/((5/10+1)*10)=380小时。
这就意味着这类设备在每月600小时的工作时间内,每台设备能够持续坚持380小时无故障工作。
管理目标:
平均无故障间隔时间这个管理指标,体现的是设备连续正常工作的能力,表现出设备可靠工作的能力,我们通过它,进而帮助制定合理的设备生产计划和检修计划。
管理分析:
平均无故障间隔时间,这是一个设备可靠性的重要参数,统一计算出的设备平均无故障时间,可以帮助我们进行阶段生产产量预计和设备检修总体规划,单台设备计算出的设备平均无故障间隔时间,能够帮助我们更合理地安排好具体的生产计划和详实的设备维护维修计划。当然这个平均无故障间隔时间指标,我们只能够在设备制造厂商的工艺基础上去发挥我们的主观能动性,需要我们在企业内部的生产环境下去发现我们设备真正的平均无故障间隔时间,被动去按照规律安排生产与检修。当然,我们也可以主动去改变,比如针对其具体故障,研究设备的技术改造,来延长这个参数,从而提高生产设备的可靠性。
针对MTBF,我们有很多深入细致的工作可以开展,我们详细记录每次故障时的发生的时间、设备故障表现、故障原因、解决方法、所需工时、停机时间等,我们进而关注每类故障的发生周期,从而可以通过分析整理出:设备点检项目和点检标准;估计零件的使用寿命,确定最适当的点检周期和修理周期;制订计划检修标准;制订或修改运行操作标准;技术改造设备,提高设备的可靠性。
有效性分析
平均无故障间隔时间的获取,我们可以清楚知道,需要准确获取三个方面的参数,故障次数、故障停机时间和设备生产作业时间。当管理的设备数量很多的时候,每天获取这些时间的工作量就很大,如果有SCADA系统对管理设备进行故障、运行时间的自动统计,当然最准确,但无疑,投资是巨大的。在一些企业里就采用了变通的方法,比如设定设备日标准工作时间,一般范围在21小时到24小时之间,主要考虑的因素有:一般性的日常维护、岗位交接班、操作工人吃饭时间、阶段检修等因素消耗的时间;具体取值,不同行业和企业,影响的因素不同,定的时间也不同。这样就不用花代价去准确记录每一次实际的工作时间,把重点放在故障发生的详细跟踪记录上。
如何确保每次故障信息记录的准确性,达到管理分析的目标,这就是每个企业关注的重点,我们提供的具体方法也需要针对企业的管理、使用、维护、维修之间的责任关系来确定。
同时该项参数的统计计算工作量很大,尤其要落实到具体设备上,其工作量也就更大了,通过人工方式来完成,其统计速度、准确性都成为问题,这就需要管理信息系统来帮助我们完成数据的统计工作。
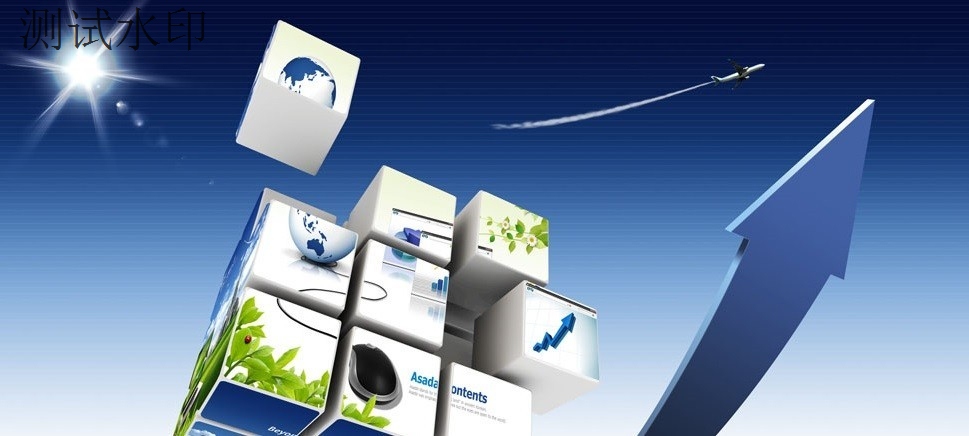
停机时间
关于停机时间,查了一些书籍,也没有一个比较统一的介绍,在实际的管理中,停机有很多种类型,在本节里,就不对各个停机类型分节讨论,就用“停机时间”这一个小节来分别讨论,方便我们进行比较和提高认识。通常来说从停机原因的角度来说,我们可以把停机大体上分成三大类:生产停机、设备停机与自然停机,其中生产停机主要包括:待料停机(由于等待原料而导致的设备停机)和质量停机(由于生产产品质量原因导致的停机)等等;设备停机主要包括:故障停机、计划检修停机、维护停机等等。自然停机主要包括停用、闲置状态、备用等的设备停机状态。
管理概念:
等待停机时间:在生产计划作业时间内,由于原材料准备不充分、生产计划安排协调不完备,出现等待材料、等待生产工序协调导致的设备停机时间。
质量停机时间:在生产计划作业时间内,由于工艺技术等原因影响产品质量问题,导致的设备停机时间。
故障停机时间:在生产计划作业时间内,由于设备故障原因导致无法生产的设备停机时间,包括设备状态恢复过程所消耗的时间、等待检修所需备件与工具的时间和等待检修所需要人员的时间等等。根据责任人不同,还可以细分为操作故障停机时间和设备维护故障停机时间。
计划检修停机时间:根据设备领部件磨损裂化特性,定期开展设备功能性恢复检修的停机时间。
维护停机时间:根据设备的润滑保养要求,开展日常维护保养工作来实现保持设备性能状态的工作给出的设备停机时间。
自然停机时间:设备由于生产任务不饱和、生产工艺改变或者生产冗于要求的设备备用等情况下导致设备的停用或者闲置的停机时间。
计算方式:
生产停机时间=等待停机时间总和+质量停机时间总和。
设备停机时间=故障停机时间总和+计划检修停机时间总和+维护停机时间总和。
自然停机时间=设备停用时间总和。
管理目标:
提出等待停机时间,主要是关注生产准备不足导致企业的生产损失,让生产计划者更好的安排生产计划工作,最大程度提高设备的利用率。
质量停机时间,记录的是调整产品质量时发生的停机,让生产工艺者们重视在生产配方和生产工艺流程上也存在直接的生产损失,用于约束和督促生产工艺员搞好产品设计工作,而且质量停机时间发生,背后还会有更大的生产材料损失,这对于生产制造业来说就很重要。
故障停机时间,用来记录设备故障导致的生产停机耽搁,直接反馈设备维护不到位或者操作不正确导致的生产损失,从责任角度来说,维护不到位可以落实到设备维护者上,操作原因导致的故障,这把责任落实给设备操作工上,该时间可以根据企业责任分工情况采取统一或者分开计算。
计划检修停机时间:把这个时间计算出来,其实就是要求设备管理者不断去总结设备的自然规律,找到最经济的计划检修时间,从而有利于平衡生产时间,追求生产效益最大化。
维护停机时间:把这个时间计算出来,也是要求设备管理者不断去总结设备的自然规律,找到最经济的维护时间,从而有利于平衡生产时间,追求生产效益最大化。
自然停机时间:是用来记录由于生产能力剩余余量,反馈企业资产投资的利用效率;从另外一个角度来说,对于追求可靠性高的关键性生产来说,该数据体现的是企业抗击生产风险的能力。
管理分析:
停机时间的分门别类,主要是便于发现生产过程中的问题根源,以及体现企业当前的主要问题所在,三个大的停机分类不一定适合所有行业,比如生产停机时间,比较适合生产制造业,这对全面提高生产效益来说,显得比较重要,对于发电、输配电、能源行业就意义不大了。
对于设备停机时间的掌控,其中关于减少故障停机时间,探索设备计划检修时间和合理规划设备维护时间,这是设备管理者一项巨大的挑战,在保持好设备性能状态下找到最短的设备停机时间,这对提供设备生产时间,提高设备利用率来说是最好的贡献。
对于维护停机时间来说,对于移动工作设备,我们应该全面利用设备的装卸工作时间、能源补充的时间、交接班的时间去开展部分维护工作;对于固定工作设备,我们应该在设备平稳生产过程中,在物料更换和工装具更换等时候,开展设备维护工作,尽最大努力,减少安排单独的维护停机时间。
对于自然停机时间来说,我们的很多企业关注投用设备的状态保持,很少去关注已经停用的设备,认为停用就听用了,需要的时候在启用,其实,我们存在停用的主生产设备,除了冗于考虑外,意味着我们投资规划失误,把主生产设备的自然停机时间反馈出来,让生产成本中不仅仅只包括生产中设备的成本与折旧,同时也考虑为了保证生产做的多余投资设备的折旧,计算出更准确的生产成本消耗,也能够让我们在做资产投资计划的时候更谨慎。
一些企业,为了把库存供给的责任也体现出来,提出了等待备件时间,就待件责任来说,固然维修更换工作由于备件缺失导致工作延后的事实出现了,但不肯定一定就是备件存储责任,这主要还和检修计划的安排有密切关系,这个指标很难去参与考评,所以在此特别提出,并不建议企业过度关注。
有效性分析
无疑要利用这几个停机时间来管理资产,实现对这些时间的记录,以及记录的准确性将是最大的难点。这些停机记录,其首先是定性判断,然后才是数字信息记录。在整个生产过程和设备管理过程中,要准确记录以上几个停机时间,有两个需要首先解决的难点,1、首先能够拿出让生产管理者、设备管理者、设备维护者及设备操作者等相关责任主体都认同的鉴定标准,这样才能解决实际记录过程中的争议,避免扯皮现象出现。2、要有合理的流程来跟踪以上各个停机状态,落实确定的人员来在以上状态出现的时候进行记录,并把信息准确反馈到管理者面前。
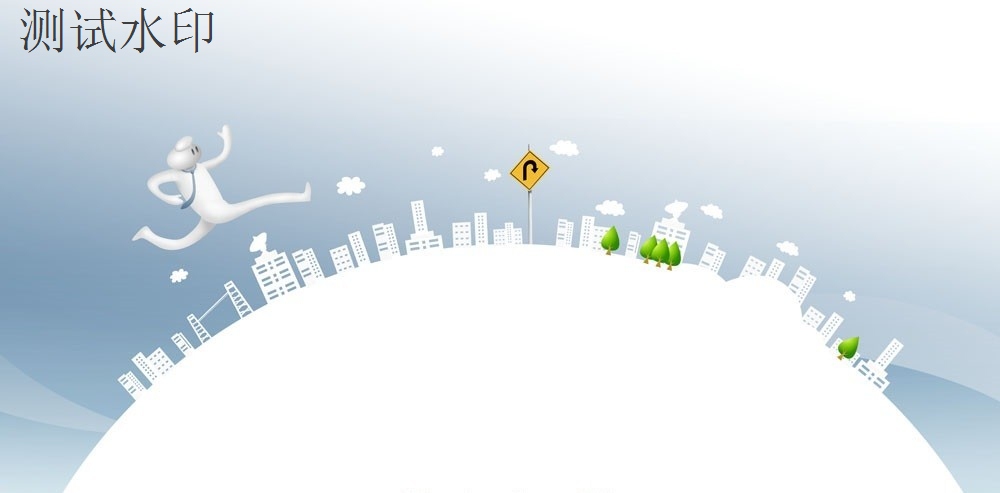
设备利用率
管理概念:
设备利用率是指单位时间内设备实际使用情况或者设备生产效果占理论上的设备使用情况或者设备生产效果的百分比,是指设备被用来投入使用的效率,反映设备工作状态及生产效率的技术经济指标。
设备利用率这个指标,根据行业特征不同不同,大家对其关注点也不一样;比如,对于制造业,企业关注设备发挥的效率,关注设备在规定时间内生产的产品数量和理论产能的比较,用于判断生产设备产能的发挥效率;而对于移动设备与能源行业生产设备,等无法准确利用其的生产结果来衡量其使用效率的设备,更关注设备投入生产的时间与理论工作时间的对比。总结一下,行业内经常性有以下提法:
定义一:单位时间内设备的实际生产产量和理论生产产量的百分比值。
定义二:单位时间内设备的实际运转时间和计划运转时间的百分比值。
定义三:具体时刻设备投入运转的台数和总设备台数的百分比值。
计算方式:
定义一:设备利用率=实际产量台总和/(单台理论小时产量*日标准工作小时数*设备总台数)*100%;
计算具体举例说明:
10台设备,每天每台设备工作实际可用小时数是20小时,每小时的台产量是500件,完成产量1万件/台;其每台理论小时产量是600件,日标准工作小时数是22小时。
设备的利用率=(10*20*500)/(600*22*10)*100%=75.76%;
定义二:设备利用率=设备实际工作时间总和/(日标准工作小时数*设备总台数)*100%;
计算具体举例说明:
如上例:10台设备,每天每台设备工作实际可用小时数是20小时,每小时的台产量是500件,完成产量1万件/台;其每台理论小时产量是500件,日标准工作小时数是22小时。
设备的利用率=10*20/(22*10)*100%=90.909%;
定义三:设备利用率=(运转台数/设备总台数)*100%;
如上例:10台设备,每天每台设备工作实际可用小时数是20小时,每小时的台产量是500件,完成产量1万件/台;其每台理论小时产量是500件,日标准工作小时数是22小时。如果在评估的时候,10台设备有2台没有投入使用。
设备的利用率=8/10*100%=80%;
设备总数可以根据我们对考核者的考核要求来定,当设备总数是1的时候,就是单台设备的利用率。
管理目标:
在资产密集型企业当中,设备投资常常在总投资中占较大的比例。因此,设备能否充分利用,直接关系到投资效益,提高设备的利用率,等于相对降低了产品成本。所以,作为企业的管理者,很关注该指标。提出设备利用率管理指标,我们认为主要体现设备的生产被利用效率。通过该指标,推动管理者加强整体计划管理,首先提高设备出勤率,保证企业生产效益;然后改善及完善生产条件,减少生产过程损失,提高生产时间内的设备效能。设备利用率指标针对的可以是具体一台设备、一类设备;同时可以是管理者的所有设备、也可是管理者的部分重点设备。
管理分析:
讨论设备利用率,其核心是提高企业投资回报率,希望企业投资能够实现预测的收益,有效控制企业发展。
定义一表达设备的利用率,体现的是设备产能效率和设备出勤效率共同影响下的设备利用率,尤其对于生产设备有产能标准衡量手段的时候,加上产能效率这个角度上来说,比单纯从设备出勤率考核设备利用率更严谨、更全面,当然,这种情况只能够生产自然环境相对比较固定的前提容易把握,比如连续生产线的制造行业、连续输送行业等等。这个指标主要用来同时考核设备维护能力和生产组织能力,就拿上例来说:
设备出勤效率=实际工作小时数/理论工作小时数*100%=20/22*100%=90.909%;
设备产能效率=实际(小时)产量/理论(小时)产量*100%=500/600*100%=83.33%;
设备真正的利用率=设备出勤效率*设备产能效率=90.909%*83.33%=75.76%;
这样的指标更能够让管理者从设备维护和生产组织两个方面去分析问题,寻找问题根源和提出解决问题的方法,有效提高管理水平,定义一考虑对设备的利用效率影响因素是最全面的,这个角度思考设备利用率值得推广。
定义二表达设备的利用率,体现的就是设备的出勤效率,侧重点还是关注设备的维护水平和总体生产计划安排。当然这种设备利用率的计算方式,还是被产量受生产时间外生产环境条件影响很大的行业广泛采用,比如运输行业,在标准装载量和运输速度前提下,车辆的实际运输量除了车运输时间外,还受运输距离的影响;如发电行业,发电量除了与发电机组的运行时间有关,其中还受其它重要因素所影响,如火电和当前燃煤热量情况有关、风电和当前风力有关、水电与当前水流量有关,无法制定出标准时间产能。我们主动能够控制的就是设备的可靠性,保证计划时间内的稳定生产。定义二在考核设备的利用率来说,确实遗漏了部分影响因素,是否作为利用率的评价标准其实主要看其他因素对利用率准确性的干扰程度,能够达到90%以上,就可以了;当然如果需要准确率更高一些,可以尝试建立标准产能,考虑其它相关重要影响因素,进行处理。一些行业采用折算成标准产品的标准产能,把不同产品的产能折算成设备的标准产品的产能,就可以消除产品差异带来的影响,这点水泥行业就采用过。
定义三表达设备的利用率,体现的是及时设备利用状态,企业资产管理的角度上来说,我们容易关注重要设备的即时状态,让资产责任人有压力与动力去维护好设备,保持所有时刻的设备状态,如同故障率的描述一样,也给予了责任人一个管理投机的可能。用定义一作为指标来考核,随机性、偶然性很大,所以一些企业就把考核点定义在每月月末的固定时间,所有责任者就会在考核点到的时候全力去开动设备,这有虽然一定的积极意义,但这样会掩盖考核期过程中管理设备停产情况,丢掉了设备利用的真实性。总体来说,定义一应该是管理者关注的内容,对实现管理目标有一定意义,但如果要作为考核指标,缺陷大于指导意义,很难操作与推行。适合管理人手不够、管理统计记录手段薄弱、标准化水平低的管理阶段和企业的简单管理。
有效性总结
对于设备故障率这个指标,无论采用上面那一种计算方式,具体数据都来自设备使用与维护一线工作人员,而我们考核的责任主体,又常常就是设备使用者或则设备维护者自身,所以,信息如何被真实反映,就是我们管理者必须认真考虑的问题,对着一个无真实性可控的指标进行考核,我们也只是在粉饰太平,只是在浪费时间,在自欺欺人。我们在好几个企业中都有类似发现,从一线管理者的工作方法、管理思路、检修费用、生产产量等角度去分析,我们认为管理好的一线管理者,他们上报的设备故障率居然要比其它同等角度反馈信息差好多的部门要高几许,实际现场调查设备状况和我们推理得到的结果是一致,为了搞清楚这种矛盾情况出现的原因,就召集过来当面沟通,他说,“就我提报的故障率,是我们现场实际的数据,我也不敢去做假,因为还有相关其他信息进行限制,所以我只有实情实报”。而他管理者也有不泛坦率者这样说:“我没有办法控制故障,整天都在忙碌,所以你们需要什么数字,我只有到时候就给你们什么数字,也考虑不过来上报数据的合理性,如果按照实情汇报,还不罚倒我啊,反正如果查出来,在认罚也一样!”。
所以,选择考核指标,我们首先要考虑我们获取信息、统计信息的有效性和可控性,没有这个前提,我们玩的就是简单的数字拼凑游戏,没有管理效果可言。